Installation of driving anchors and piles UZAS-2
To install the piles, which are one of the main structural elements of the structure, several types of equipment are used. Concrete, metal or reinforced concrete piles are immersed in the ground with diesel or hydraulic hammers, vibratory pile drivers or pile-driving installations. Having certain advantages, all samples of such equipment are not without some drawbacks. For example, the impact method of pile driving is associated with prolonged loud noise, vibrations, etc. For a long time, domestic and foreign engineers were looking for a way to reduce the negative impact of the installation of piles on the surrounding infrastructure and people.
The original project, designed to solve existing problems, was developed in the second half of the eighties. Specialists from the Perm Polytechnic Institute (now Perm National Research Polytechnic University), led by Professor Mikhail Yuryevich Tsirulnikov, developed the original construction machine. For several decades M.Yu. Tsirulnikov was engaged in the creation of promising artillery guns of various classes, intended for use in the army. Later, the accumulated experience was proposed to be used in a new field.
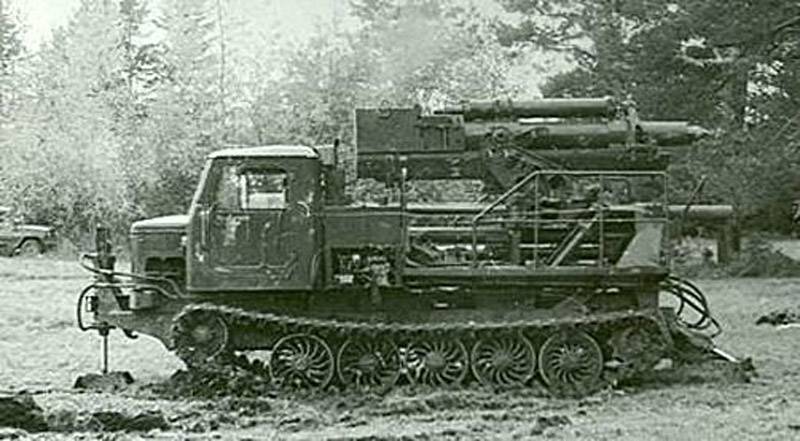
General view of the installation of UZAS-2 in the transport position. Photo Strangernn.livejournal.com
A promising project of construction equipment received the name UZAS-2 - "Installation of driving anchors and piles." The project was based on an original proposal concerning the principles of pile driving to the ground. All existing samples of a similar purpose could sink a pile only gradually, at some speed or another. For example, diesel hammers perform this task with a long series of strikes. The new model, in turn, had to set the pile to the required depth in one or two blows. To obtain the required energy indicators, it was proposed to use a slightly modified artillery gun of the existing type. That it should literally "shoot" the pile into the ground.
Based on an unusual proposal, the employees of the Institute of Industrial and Industrial Engineering under the guidance of M.Yu. Tsirulnikova soon formed a practically applicable method of installing building elements, characterized by high efficiency. The use of so-called pulse indentation allowed 2-2,5 times to increase the pile driving depth with one shot compared to a different use of the same energy. At the same time, it was possible to use the maximum possible number of ready-made components and assemblies.
The design of the UZAS-2 installation was completed in the 1988 year, soon after which the assembly of the experimental equipment began. By the time this work began, the authors of the project managed to interest the leadership of the oil and gas industry. Thus, it was proposed to test the original sample of construction equipment at the construction sites of the Permneft enterprise. The assembly of the experimental equipment was carried out by one of the workshops of this enterprise with the active participation of specialists from the PII and the Perm plant named after Lenin. The result of this cooperation in the near future was the appearance of three self-propelled units at once capable of driving piles.
One of the main ideas of the project UZAS-2 was the use of ready-made components. First of all, it concerned the driving system, which was planned to be built on the basis of an existing artillery gun. In addition, during the construction of experimental equipment, existing samples of self-propelled equipment were used, which allowed special equipment to be moved independently to the place of work.
As a basis for self-propelled installation UZAS-2 was chosen serial skidding tractor model TT-4. This machine had a tracked chassis and was originally intended for transporting trees or packages of whips in a semi-submerged state. During the construction of the experienced UZAS-2, the tractors lost their special equipment of the original model, instead of which the means of pile driving were mounted. At the same time, significant changes in the design were not required, since all such equipment was installed on the existing cargo area.
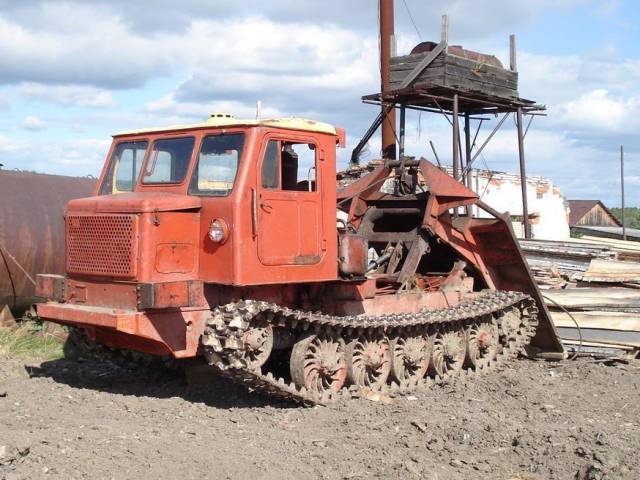
Trailer TT-4 in the original configuration. Photo S-tehnika.com
The tractor TT-4 had a frame with a low frame height, which had space to install the target equipment. In front of the hull provided for the installation of the cockpit and engine compartment. The entire upper part of the hull behind the cabin was given to the equipment of the required type. Right inside the cab on the longitudinal axis of the tractor was placed the engine compartment. Due to the large size, the engine and its radiator required the use of an additional casing with a grill protruding beyond the main cabin. Below the engine and inside the case were placed various transmission units.
The skidder was equipped with a diesel engine A-01ML with power 110 hp With the help of a clutch, manual gearbox, rear axle, final gears and transfer case, the engine was connected to the drive wheels of the chassis, the winch used for skidding, and the hydraulic system pump. A reverse gearbox allows you to choose from eight forward and four reverse speeds. For control, a planetary gear with belt brakes was used.
As part of the chassis tractor TT-4 had five road wheels on each side. A characteristic feature of the rollers was a design based on curved spokes. The rollers were blocked with two carts with their own springs: two were placed on the front carriage, three - on the back. In front of the hull housed the steering wheel, significantly remote from the first track roller. In the stern was leading. The large diameter of the rollers allowed to abandon the individual support rollers.
"Installation of driving anchors and piles" during construction received leveling systems, mounted directly on the frame of the existing chassis. To the front of the machine attached the removed unit with a vertically located hydraulic cylinder. Two more jacks were in the aft part and had to be lowered to the ground by turning. This design of additional supports allowed to keep the machine in the desired position during operation.
The most interesting part of the UZAS-2 machine was located on the landing gear of the chassis, previously intended for fastening a skidder. The site design was slightly modified, and in addition, it had a small fence. On special mounts it was proposed to mount the artillery unit directly responsible for driving piles. The basis of the swinging unit was a frame of three longitudinal tubes connected by additional elements of the corresponding form. In the transport horizontal or working vertical position, the frame was transferred using two hydraulic cylinders.
As a means of driving piles, it was proposed to use the X-NUMX-mm cannon of case artillery M-152 (GAU Index 47-П-52). This is a tool developed by the Special Design Bureau of the plant No. XXUMX (now “Motovilikha Plants”) with the most active participation of M.Yu. Tsirulnikov, produced serially from 547 to 172 years and for some time was used by the Soviet army, after which it gave way to newer systems. The project UZAS-1951 proposed some alteration of the existing tools of the obsolete type, after which it could serve as a source of energy for immersing the piles into the ground.
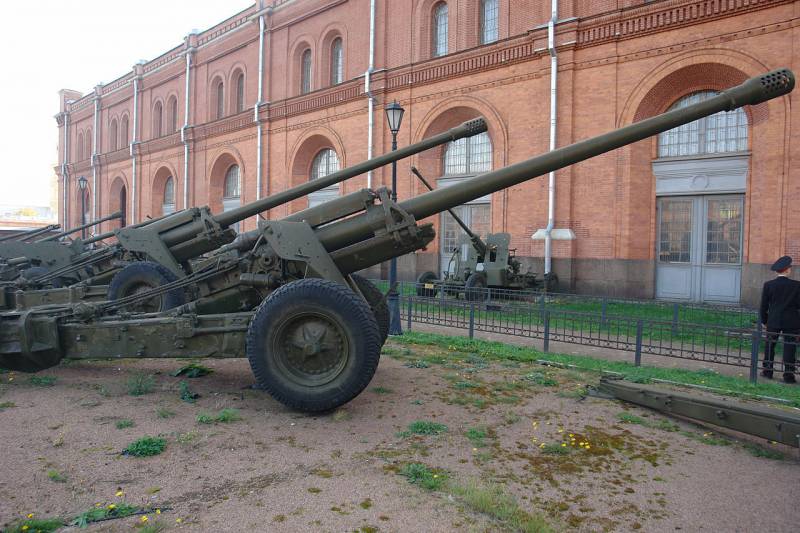
The M-47 cannon in the Military Historical Museum of Artillery, Engineering and Communication Troops (St. Petersburg). Photo of Wikimedia Commons
One of the positive consequences of the implementation of the new project and the mass construction of such equipment could be savings on the disposal of existing tools. In the fifties, the Soviet industry built the entire 122 M-47 cannon, which were subsequently withdrawn from active operation and sent to storage. In the future it is weapon had to go for recycling, but the construction of piling facilities allowed to delay this moment, as well as get some benefit from the decommissioned products.
In the original version, the M-47 corps artillery gun was a 152 mm caliber gun with a 43,75 caliber barrel. The gun was equipped with a wedge bolt, hydraulic recoil devices and a muzzle brake. The barrel group in the form of a barrel, a breech and a casing for fixing in the cradle with the help of trunnions of the latter was mounted on a carriage consisting of upper and lower machines. The upper machine was a U-shaped device with mounts and actuators pointing guns, while the lower was equipped with beds, wheel travel, etc. The mast design allowed shelling of targets in a horizontal sector with a width of 50 ° at elevation angles from -2,5 ° to + 45 °. The carriage was equipped with an armor shield. The maximum firing range reached 20,5 km.
Within the framework of the USZAS-2 project, the existing M-47 cannon should undergo noticeable changes. First of all, it was deprived of the lower machine and other elements of the mast. Also removed the armor shield, sight, muzzle brake and a number of other more unnecessary units. The upper machine, cradle and other elements of the artillery system were proposed to be installed on the swinging frame of the self-propelled unit. In this case, the barrel was blocked in a predetermined position, parallel to the tubes of the swinging frame. To reduce the size of the entire machine assembly and reduce energy performance to the required level, it was decided to seriously trim the existing trunk. Now its muzzle end insignificantly stood for the level of recoil devices.
Together with the modified tool for driving piles it was proposed to use the so-called. rammer This device was designed as a large piece of variable shape. The shank of the rammer had a cylindrical shape with an external diameter of 152 mm, so that it could fit into the gun barrel. The head tip of the device was significantly larger and was intended to ensure contact with the driven pile. Also in the composition of the rammer was so-called. interchangeable camera located on the shank. It was proposed to use to install the powder charge. The use of standard shells from 152-mm artillery shots was not provided.
Arriving at the place of work, the builders had to install the UZAS-2 machine in the required place and use the jacks to place it in the correct position. Next, the frame was raised with an artillery unit, and a ram associated with a pile was placed in the barrel. After that, the installation operator gave a command to fire, and the pile entered the required depth under the action of powder gases. The latter was changed using a variable charge.
In the 1988 year, several self-propelled units of the UZAS-2 type were built by several Perm enterprises at once, which were immediately planned to be put into limited operation. To test this technique was proposed simultaneously with the construction of certain objects. In the late eighties, Permneft and various divisions of this structure were actively engaged in the construction of new facilities, so the installation of blocking anchors and piles did not risk losing their jobs. They had to participate in the construction of a variety of new projects for the Polaznaneft oil and gas production department and the Zapsibneftestroy enterprise.
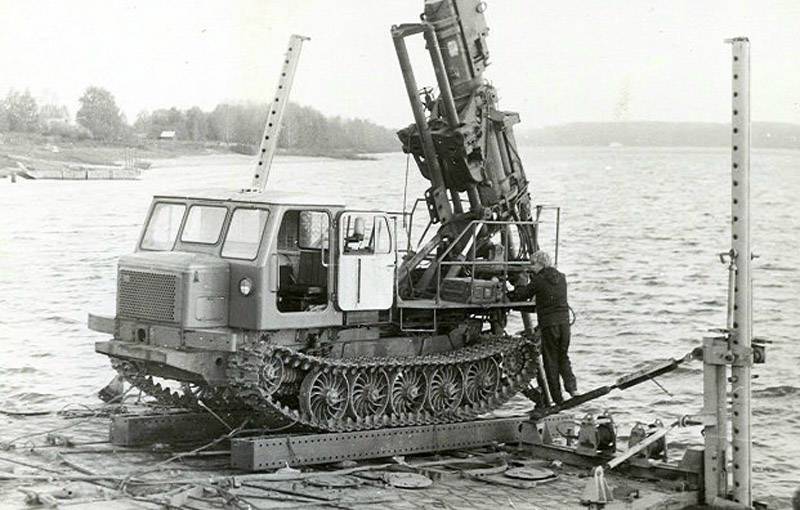
UZAS-2 on the pontoon, allowing to drive piles into the bottom of the reservoir. Photo Strangernn.livejournal.com
One of the first real problems solved by the UZAS-2 installations already in 1988 was the pile driving for the construction of two foundations of the Zapsibnefttestroy pumping units. During these works, builders had to drive piles into the permafrost. Despite the complexity of such work, the specialists quickly installed all the necessary piles, giving fellow builders the opportunity to continue construction. According to some data, converted drill pipes were used as piles for such construction.
In the future, similar work was carried out at other sites in different areas. It was found that the minimum depth of driving is 0,5 m. When driving into medium clay soil, a pile could be sent to a depth of 4 m with a single shot. When working with more complex soils, a second blow on the pile could be necessary. At the same time, most of the tasks were successfully solved with a single shot at the pile. Piling one shot allowed you to speed up the work. During actual operation, it was found that one installation of the UZAS-2 can drive up to ten piles per hour - up to 80 per shift.
A characteristic feature of the UZAS-2 system was the minimum noise and vibration produced during operation. Thus, the existing diesel hammers at work create a series of loud pops and spread powerful enough vibrations around the ground that can threaten the surrounding structures. Installation based on the gun M-47, in contrast to such systems, made only one or two blows to the pile. In addition, the blocking of powder gases inside the barrel further reduced noise and negative effects on surrounding objects. During construction work in the Perm Car Repair Plant, the installation of UZAS-2 hammered piles at a distance of 1 m and less from existing buildings. Reportedly, despite the many shots and the execution of the tasks, none of the nearest buildings were harmed, and all their glasses remained in their places.
With all its advantages, the UZAS-2 system had some drawbacks. Thus, the need to use existing tools could to some extent complicate the production of serial equipment due to bureaucratic and other factors. In addition, the proposed machine design imposed certain restrictions on the length of the pile being driven. It should be noted that with the further development of the project, the existing shortcomings could well be corrected.
In the course of theoretical research and practical development, specialists from several organizations studied the possibility of using UZAS-2 for solving special problems. For example, the driving of piles in the conditions of a bog was practiced. In this case, a shot was required to lead a pile through a layer of water, silt, etc., after which it had to enter solid ground. It was also proposed to penetrate several metal electrodes, along which a high-voltage electric current should be passed. Such an impact led to soil compaction, which could be used, for example, during construction on slopes that require a certain reinforcement. This did not exclude the shooting of piles in non-standard positions of the artillery unit.
Of particular interest is the design of a system designed for driving piles into the bottom of reservoirs. In this case, the self-propelled tracked vehicle had to be delivered to the work site by means of a towed pontoon. On the latter, some special devices and means of securing the UZAS-2 installation were placed. Especially for the pontoon version of the installation, a special control system was developed to ensure the correct shot by the pile. The special device had to monitor the position of the pontoon and the artillery part and take into account the available pitching. When the desired position was reached, the device automatically gave a command to the shot, thanks to which the pile went to the bottom with minimal deviations from the desired trajectory. After passing through the water, the pile continued to move in the ground and reached a predetermined depth.
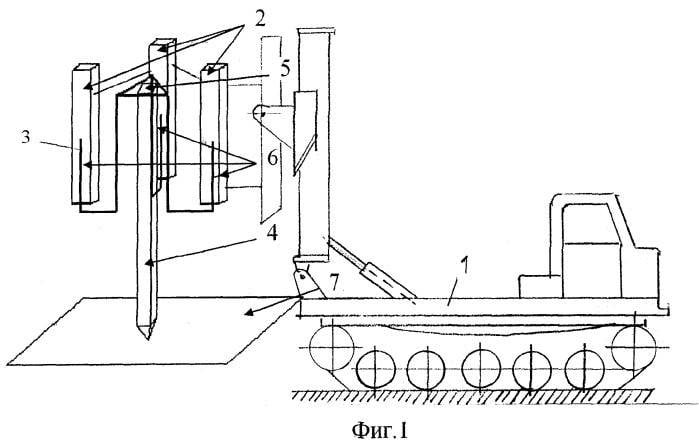
The modern version of the multilateral installation of pile driving, drawing from the patent RU 2348757
Operation of the three built installations UZAS-2 lasted until the year 1992. During this time, the cars managed to participate in the construction of many different objects of the extractive industry. According to the results of such exploitation, more than interesting conclusions were made. The possibility of driving up to 80 piles per shift gave an increase in labor productivity 5-6 times in comparison with traditional systems of similar purpose. The cost of work was reduced in 3-4 times. Thus, the operational and economic benefits of the original technology fully compensated for all minor flaws. The installation of USZ-2 in practice showed all the perspectives of the original proposal by M. Yu. Tsirulnikov and his colleagues.
Operation of the three pilot plants of the UZAS-2 was completed in the early nineties. In another period of domestic stories the project could have continued, with the result that the construction industry would have mastered a large number of new types of machines with high performance, capable of quickly and cheaply driving various types of piles in various constructions. However, this did not happen. The collapse of the Soviet Union and the ensuing problems put an end to many promising developments.
The further fate of the three UZAS-2 machines is authentically unknown. Apparently, in the future they were disassembled as unnecessary. In addition, the TT-4 tractors could have been converted according to the original project and returned to the corresponding work. New models of such technology have not been built. For two decades now, Russian builders have not used artillery piles in their work, using traditional systems of construction.
However, the idea was not forgotten. For many years, the specialists of the Perm Polytechnic Institute / Perm National Research Polytechnic University continued to develop the original proposal, resulting in a substantial amount of theoretical materials, several projects and patents. In particular, it is proposed to use a multi-barreled system, in which pile driving is carried out by simultaneous undermining of several charges in three trunks. As part of such an installation, it is proposed to use a single large bollard, simultaneously interacting with all three trunks.
In the eighties, the original idea of increasing productivity when driving piles reached practical use and made a significant contribution to the construction of various industrial facilities. New projects have not yet achieved such success, remaining only in the form of a set of documentation. Nevertheless, it is impossible to exclude such a development of events in which new projects of using artillery while driving piles will nevertheless reach full implementation and use in practice.
Based on:
http://a-economics.ru/
http://izobretatel.by/
http://traktorbook.com/
http://s-tehnika.com/
http://strangernn.livejournal.com/
http://cyberleninka.ru/article/n/neobhodimoe-uslovie-vertikalnogo-zastrelivaniya-stroitelnyh-elementov-v-grunt-iz-mnogostvolnoy-artilleriyskoy-sistemy
http://findpatent.ru/patent/234/2348757.html
Information